One of the best ways to reduce the energy a home or building consumes is careful consideration of the envelope. Our journey to creating the most efficient building enclosure/envelope began in the mid 1990’s with the first version of the Matrix Wall™. We regularly adjust this wall system, incorporating what we’ve learned and what new sustainable materials may be available to reduce consumption and increase comfortable living. In 2017 this journey took us to Poland to learn more about wood fiber insulation from Steico. In 2018 we landed in the Netherlands to explore semi-automated custom tooling. Fast forward (let’s all just skip 2020) to 2021 – welcome to High Performance Made Easier!
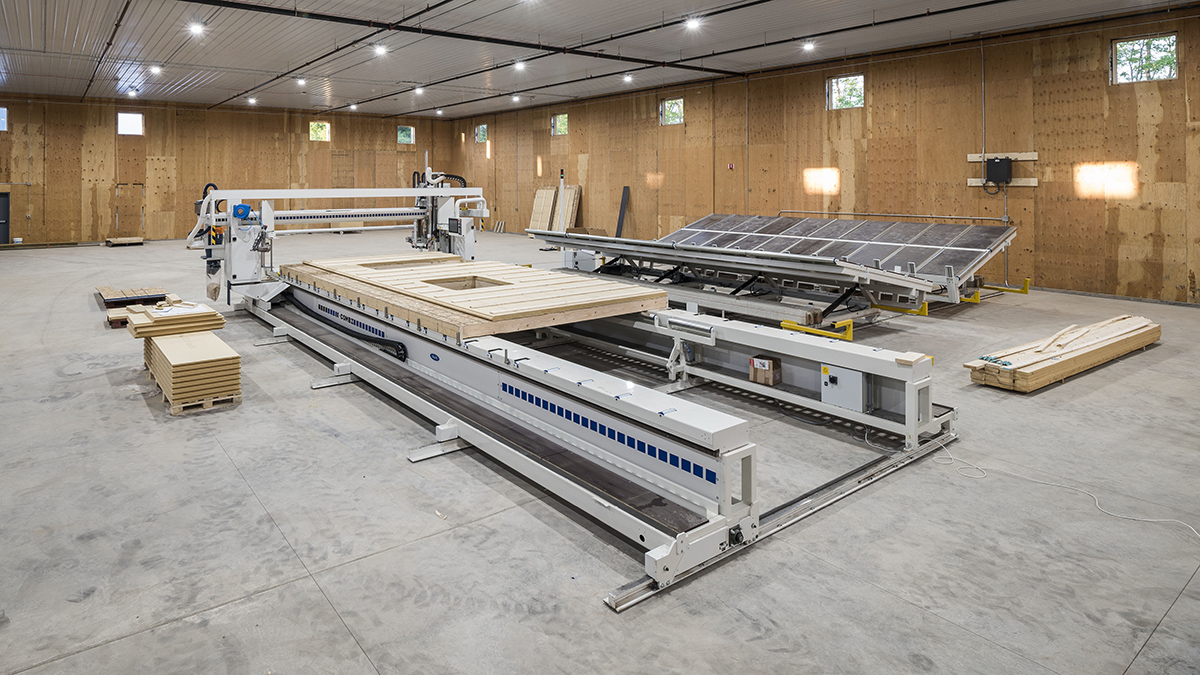
We’ve added a new building with new semi-automated tooling to produce the latest evolution of our Matrix Wall™ systems–we’re calling it HPEz, High-Performance Made Easier–to our campus in Farmington NY. Earlier this month we ran the very first wall panel for calibration and plain old getting-to-know-the-tools practice:
Designed and crafted in the USA with the planet in mind for over 15 years, our pre-panelized wall and roof systems are customizable to each project. The climate-controlled production environment means weather doesn’t slow down work or impact components. It’s also a bonus for our carpenters and operators to be under the roof and on our main campus more often.

Using modern software, we’re digitally designing each pre-panelized system, helping to identify and coordinate some of the trickier interaction details prior to installation. This planning also allows a reduction of material waste during construction (off-site and on-site). Plus, the standard system has open cavity panels arrive on-site with 1/2” sheathing, continuous outboard wood fiber insulation, a weather-resistive and vapor open barrier, and strapping. We can produce custom panels including closed cavity as requested. They’re ready for raising, fit, and finish in far less time than traditional on-site framing.


Bryan from our timber frame engineering team is spearheading the engineering process with wall details/programming for the enclosures. He’s joined in the HPEz shop by newest team members Adam, Max, and John as well as a rotation of long-time coworkers of our carpentry team.

From overseas to under roof, we hope you’ve enjoyed this glimpse into our journey and join us in this moment of excitement. We’re optimistic that this latest step in upgrading and improving our prefabricated wall system will allow you and yours greater enjoyment in more efficient, planet-friendly shelters. There is so much to share on HPEz–reach out if you’d like to know more or have a project you’d like to chat about.